5 Most Common Manufacturing Processes for Plastics
- Axam Design
- Apr 24, 2023
- 2 min read
Updated: Jun 1, 2024
Plastic products have become a part of our everyday lives, and they are used in a wide range of products, including electronics, automotive parts, toys, and more. The plastic manufacturing industry has developed various processes to create these products efficiently and cost-effectively.
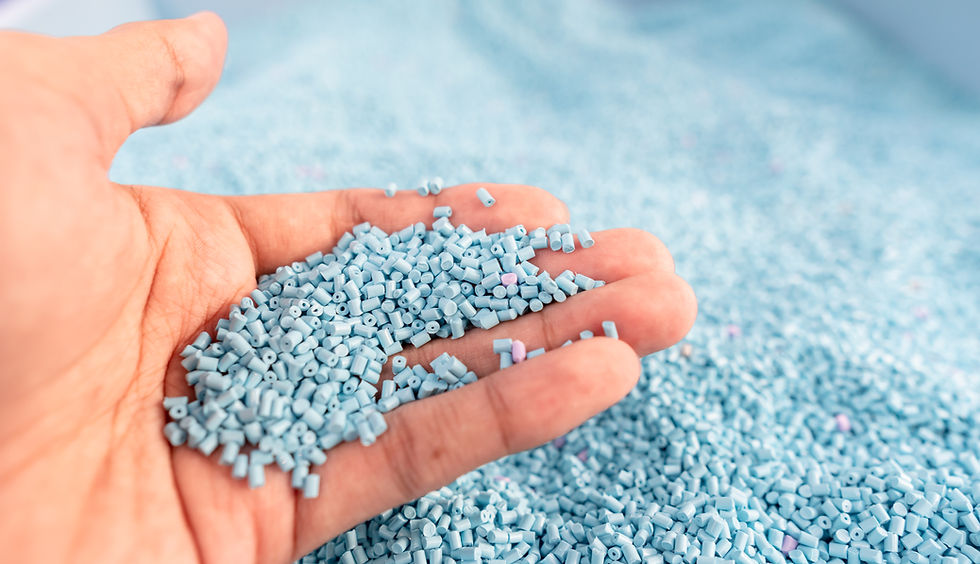
Here are 5 of the most commonly used manufacturing processes for plastics :
INJECTION MOLDING : Arguably the most popular manufacturing process due to the fact it's a highly automated and precise process, making it suitable for high-volume production of complex shapes. It involves injecting molten plastic into a mold cavity that is made of two parts (the cavity and core,) which defines the shape of the product. Once the molten plastic is injected into the mold, it cools and solidifies, and the mold opens to release the finished product.
EXTRUSION : Extrusion is a process where plastic pellets are melted and forced through a die to create a continuous shape, such as a tube or a sheet. The extruded product is cooled and cut to the desired length. Some common applications include pipes, profiles, and films.
BLOW MOLDING : Blow molding is a process where a hollow plastic part is created by blowing air into a molten plastic tube or parison. The tube is clamped in a mold, and air is injected through a small hole, causing the plastic to expand and conform to the mold's shape. Blow molding is commonly used to produce bottles, containers, and other hollow parts.
ROTATIONAL MOLDING : Rotational molding is a process where a mold is rotated around two perpendicular axes while heated plastic is added to the mold. The plastic coats the inside of the mold, and as it cools and solidifies, the mold is opened to release the finished product. Rotational molding is a versatile process that can produce large, hollow parts with complex shapes. Common applications of rotational molding include storage tanks, playground equipment, and automotive parts.
THERMOFORMING : Thermoforming is a process where a flat sheet of plastic is heated until it becomes pliable and then vacuum formed over a mold. The mold can be male or female, depending on the shape of the product. Once the plastic has cooled and hardened, it is removed from the mold, and any excess material is trimmed away. Thermoforming, aka. Vacuum Forming is commonly used to produce packaging, refrigerator and freezer door liners, and ice cube trays.
There are advantages and disadvantages, engineering limitations, and design considerations for each of these manufacturing processes. The choice on which process to go with depends on the product's intended function, design, material, budget, and quantity needed.
TL ; DR
There are various plastic manufacturing processes that have been developed to create products efficiently and cost-effectively. Injection molding, extrusion, blow molding, rotational molding, and thermoforming are the most common manufacturing processes for plastics.
If you're looking to bring a plastic product to life, working with a product design and development firm like Axam Design brings immense value. We can help you design a product that is both functional and aesthetically pleasing while considering the best manufacturing process to achieve your goals. Don't hesitate to contact us and let us help you bring your ideas to market.
Comments